Dishwasher malfunctions. DIY repair. Washing dishes. To repair, repair. Elimination. Scroll. The dishwasher is broken - can I fix it myself
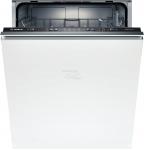
- a complex and moody mechanism. Any errors during its installation and operation can cause malfunctions and malfunctions. In order to avoid costly repairs and breakdowns of the dishwasher, you need to know all the symptoms of violations in the mechanism.
Specifications
Design and main features
The main function of the dishwasher is to remove fat and sterilize dishes by spraying it with hot water and detergent. This is achieved using an electric motor and a pump mounted at the bottom of the tank or tank.
The pump draws water from the tank and delivers a pressure of water through sprinklers that spray the dishes. Then the water simply drains back to the tank for recycling.
Of course, first of all, hot water should get into the tank. This requires an electric (electromagnetic) valve. Hot water comes directly from the water heater of your home from the water supply network. There are also models that heat water directly in the tank with an electric heater.
At the end of the cycle, water should be drained from the tank. The motor drives the pump to perform this function.
Even under the most favorable circumstances, dishwashers, as a rule, have a shorter service life than other large household appliances. Why? Well, to answer this question, let's become for a moment a little perverts, and design a torture chamber for an electric motor.
What is the absolutely worst enemy of electricity in a car? Water, right? Then let's use the engine to pump water and let's install the motor directly under the water tank. Thus, the entire flow of hot water will flow over the engine, the steam will enter the engine and it will be covered with rust. Although this is not all, let's run through the pump a few pieces of glass, large pieces of food, nutshells and seeds, so we can crack seals and working turbines, as well as make some good, unexpected shocks, suddenly jamming the engine and pump. And, of course, for maximum heat storage, let's install the engine and pump assembly in a small, cramped, steamy, dusty, poorly ventilated room, right under the tank full of boiling water. Presented a picture?
Firms
Brands
Finding out what kind of company made your dishwasher can be a bit confusing. Several large companies bought the names of their cars from different manufacturers at different times. One of the companies, D&M, makes machines for a large number of different companies, you can find D&M machines under two dozen different brands. If your car brand is not listed directly in this manual, check the following lists for your brand:
ADMIRAL: Maytag
D&M: This company made a lot of cars under various labels, including Admiral, Caloric, Chambers, Frigidaire, Gaffers & Sattler, Gibson, Kelvinator, Kenmore, Magic Chef, Modern Maid, Norge, Philco, Roper, Westinghouse, and many others.
GIBSON: Frigidaire or D & M.
IN-SINK-Erator (ISE): Kitchenaid
JENN-AIRE: Maytag
KITCHENAID: Over the years, they have had their own distinctive design. Whirlpool Kitchenaid bought them a few years ago, and now these Whirlpool machines resemble vertical service machines.
Kelvinator: Frigidaire or D & M.
KENMORE: Some of them were D&M, some were Whirlpool machines.
MAGIC CHEF: Some GE machines, some Maytag, some D & M.
O’KEEFE & MERRITT: WCI or D & M.
TAPPAN: Frigidaire or D & M.
ROPER: Whirlpool or D & M.
WASTE KING: Thermador
WHITE-WESTINGHOUSE: Frigidaire or D & M
Instruction manual
Before you start ...
Find yourself a good dealer selling spare parts for household appliances. They can be found in the yellow pages under the following headings:
Equipment
Machinery, parts and consumables
Devices, household appliances, repair and maintenance
It is worth calling some of them and asking if they are only involved in repairs, or are they only selling spare parts, or are doing both. Ask them if they offer free advice on spare parts they sell. (Sometimes, organizations that offer the sale of spare parts and services will not want to advise you.) There are a lot of official services on the market of ex-technicians who are now engaged in private repairs at home. They can be your best friends. However, if you do not want to bother them with too many questions, you need to know the basics before asking questions.
Some services also offer repair services for equipment in your home. Be careful! There may be a conflict of interest. They may try to dissuade you, even try to fix your own car. They will tell you that it is too complicated, that a special “manual” is needed for repairs, which is only available in the service department. Who do you believe me or them? Not all services act this way, but nonetheless.
If they are really trying to help you fix it yourself, and you find yourself unable to handle the problem, they may be the best place to seek repair help. Here's a good tip: after what I just said, if they sold this book to you, I guarantee that they are sincerely interested in helping the DIYers.
When you go to the spare parts store, rewrite the make, model and serial number of the dishwasher from the service plate.
Information on the nameplate
Metal plates are usually located inside the door. It can also be attached to the top edge of the door itself.
If you cannot find the plate, check the documents that came with the dishwasher when it was new. They should contain the model number somewhere.
In any case, especially if you have absolutely no information about your dishwasher, take an old spare part to the store. As a rule, a spare part can be selected by appearance or by number.
It is important to know that washing dishes in a dishwasher is not just pouring hot water on it. This is not just a mechanical or hydraulic process. It is also a chemical process. It is extremely important what detergents and rinses you use. I recommend that you use the following remedies on a regular basis:
Use dry (powder) Cascade ™. The real thing. Do not use liquid detergents. And even more so, do not use ordinary liquid hand soap.
Use Jet-Dry ™ and use it regularly. Jet-Dry ™ contains surfactants that prevent droplets and smudges on dishes. Also use a product called Glass Magic ™ to prevent stains or calcium deposits on glass surfaces.
If you live in an area with hard water, be on the lookout for any white deposits in the tank. This can be most noticeable on any black plastic part inside. This is primarily calcium deposits. They can make plastic parts brittle and cause abrasion of moving parts, as well as stains or smudges on dishes. In extreme cases, with hard water, start the machine after washing with 1/2 cup of vinegar to rinse and drain, without dishes in the machine.
These are quite specific products for which no one paid me approval. To be completely honest, there are other chemicals that can be “good enough.” But why? Very good - the enemy of all just good.
A few more proven life tips:
Every few months, do a thorough cleaning. Pay particular attention to any buildup of detergent around the door seal, especially along the bottom edge of the door. Also look for and remove calcium deposits.
If you observe a buildup of scale in the machine, you need to periodically pour about 1/4 to 1/2 cup of Lime-Away ™ or citric acid (usually available at grocery stores) into the machine and run it on the washing cycle without dishes. Repeat as many times as necessary.
Every six months or so, it is worth opening the bottom panel and checking the machine for leaks in the pallet. Also check the water shutoff valve under the sink to make sure it closes when you need it.
Every few months, open, check and, if necessary, clean the air gap of the drain hose.
Make sure you load the dishwasher correctly. Cups, glasses, bowls, etc., should be located upside down so that water does not accumulate in them. Large items must be loaded so that they do not block the nozzles of the sprayers or block the rotation of the sprayers. Silver must be securely fastened.
Repair or replace the rusty parts of the machine body. You can buy paint and restore the coating of your parts in the dishwasher. Replacing rusty housing elements costs a little, and a drain pump damaged by rusty sand or damage to seals can cost you a lot more.
Equipment
Tools You May Need
Some of them are optional.
Screwdrivers: both flat and cross, two or three sizes of each of them. It is better to use shorter ones, 100-150 mm long. For some models of later production machines, you will need Torx heads.
Instruments
Heads: You will need heads from 6 to 24. It is better to buy a ratchet kit.
Crocodile clips with wires about 12-18 cm in length, for checking electrical circuits. Surely available at your local electronics store. Cost: a few dollars for 4 or 5 pieces.
Multimeter: For checking electrical circuits. It will be enough inexpensive if it can measure “alternating voltage” and “Resistance” (with limits Rx1, RX10). It is suitable for our purposes.
Rubber bulb: For flushing water taps or draining water from a pump.
Copper pipe trimmer: If you need to remove the dishwasher from the installation site under the worktop, you may need to cut the copper water supply pipe a bit to reconnect the water when you install the machine.
Terminal clamps and electrical tape: For splicing wires.
Pliers, knife and side cutters: for cutting and stripping small electrical wires.
ADDITIONAL TOOLS
Clamp Meter: To determine if electrical components are under load and which are. Very useful, but a little expensive, and there are alternative methods. If you have them, use them, otherwise you can do without them.
Bracket mirror with extension cord: Inspect hard-to-reach places under the dishwasher and behind the panel.
Cordless screwdriver or drill / cordless screwdriver with magnetic bits: to remove the panel secured by a large number of screws. This will save you a lot of time.
the timer hangs
At the end of the program, the timer hangs at 1, and the dishes are dirty. What could be the reason?
One of the most common problems bosch owners face is the lack of a drain. It can be caused by clogging and failure of the drain pump. The reason for the occurrence of such phenomena is, as a rule, poor-quality cleaning of dishes from food debris before loading into. To avoid such troubles, make sure that the dishes are thoroughly cleaned before being loaded into the machine.
Another common problem is the lack of water pressure in the hansa dishwasher. This is usually caused by errors during installation. It should be remembered that the installation of household appliances is a rather complicated procedure, which requires one hundred percent knowledge of the basics of plumbing and electronics. Conducting it yourself or trusting unskilled workers, you run the risk of future problems with the operation of the device.
The continuous filling of a 45 cm bosch dishwasher with water, even when it is turned off, indicates that the solenoid valve for filling the water has failed. It is also often caused by the fact that dishwasher connection was produced inappropriately. Extraneous noises during the operation of the machine indicate possible malfunctions in the operation of the drain pump or wear of the stuffing box. may indicate a malfunction of the engine, which creates water pressure in the dishwasher.
Lack of water pressure in the dishwasher is a symptom of clogged sprayers. The accumulation of water under the machine, as a rule, indicates that hoses or other connections of the mechanism are leaking, overfilling occurs, or the water tank is damaged.
The appearance of any signs of a malfunction of the mechanism of the dishwasher requires immediate intervention by the masters. If the machine is under warranty, repairs are possible at the expense of the company where it was purchased. With timely troubleshooting, careful operation and careful adherence to the instructions for dishwashers, the dishwasher can last for many years. You can watch videos of dishwashers on our page.
Trouble-shooting
LOW QUALITY WASHING
This is the most common dishwasher complaint. It covers many different specific symptoms, from stains, smudges or food debris on dishes.
NO POWER; ENGINE DOES NOT START
First check the circuit breaker in the electrical panel or the fuse.
Next, make sure the dishwasher is plugged into the correct outlet.
The doors are locked so that the water inlet and sink will not start until the door is open. Make sure the door is fully closed, then the door switch will be closed. Also check that the door switch is not damaged.
Is the engine humming? If so, the engine is locked. Maybe something stuck the pump. It may also be that the pump or bearings are defective or the motor windings are damaged.
Also check the junction box with connectors for burnt contacts.
NO WATER BAY
This is usually a defective water supply valve or a clogged valve. Try to clean the filter of the water supply valve; also check the resistance of the valve coil. (Note that some Kitchenaid machines have a double valve with two solenoids. The valves should be checked as if they were two separate valves). Replace the valve if it is defective.
When replacing the water supply valve, use O.E.M. parts, or at least make sure that the nominal bore of the valve is the same as in the original machine. Spare parts may have different nominal bore diameters, which can lead to a too high or low speed of water filling into your machine.
This can also be caused by the on position of the leakage protection float switch. It may freeze or fail. It is rare, but possible, to trace a burnt contact inside a timer.
NO DRAINING, ENGINE OPERATES
As a rule, this is indicated by the poor quality of the wash (strong spots) due to cold water. This is usually a blockage in the drain line or air gap.
On GE or Kitchenaid machines, the solenoid drain valve may not work. Check the coil of this valve, as well as the timer (which controls the valve), as described in sections 6-2 (a) and (b).
Another possible reason is that a foreign object has fallen into the impeller of the drain pump or the impeller blades are broken. Disassemble the pump and check the impeller.
THE TANK IS FILLED WITH WATER, BUT NO WASTE OR DRAIN (THE ENGINE DOES NOT WORK)
If you hear that the engine is trying to start, then something has blocked it. This could be a blockage in the pump with a piece of food or glass. There may also be damage to the motor windings.
If the machine’s engine rotates in one direction only and not in the other, the start windings may have burned out, this can also be due to damage to the timer contacts.
Remove and disassemble the pump and motor. Clean everything that interferes with engine rotation. If you suspect that the engine is defective, check it.
If you don’t even hear attempts to start the engine, then in this case the timer contacts may be burned out. Test and repair it.
There is also an option to start the engine using a start relay. If the start relay does not work, it will cause similar symptoms. Test it and replace if it is faulty.
NOISY WORK
This is usually caused by broken glass or rust that has fallen into the impeller of the pump or in the spray arms. It is also often caused by worn bearings in a pump or electric motor. Damaged pump bearings are a particularly common problem in Maytag belt driven machines.
Try to remove the sprinklers and clean them of debris. This can be difficult, sometimes it’s easier to replace them.
Take the pump and try turning on the pump and motor separately. The rotation should be soft, without much resistance. Any crunching, vibration or noise indicates poor bearings or damage to the pump impeller.
MECHANICAL TIMER DOESN'T ADVANCE
This is usually due to a malfunction in the engine timer. However, first check the wiring diagram. The timer motor start circuit may have several other contacts, such as a thermostat or buttons.
The solution is to replace the faulty timer motor or restore the faulty contact. If you manage to get a restored timer, you can save several tens of dollars.
FLOOR WATER LEAKAGE
If water leaks from the front of the machine, it is usually a leak from the door seal, although there are several other suspects. Poor detergent can cause foam, which can leak even through good seals. There are also some models in which the direction of water jets that spray water past doors and seals can be in the wrong direction. You need to check for these problems first. If you still suspect that it is flowing through the door seal, try to clean the seal from deposits of detergents and dirt. If you need to replace the seals, buy a door seal kit from your dealer.
If water flows from underneath the machine, this is usually due to damage to the pump seals, but it can also leak from a hose or inlet or drain valve. Remove the bottom panel and start the machine, looking under it. Try to locate the leak by observing where water is dripping onto the floor (you can use toilet paper for this. Remember that the car has live wires and therefore, do not shove your hands while the car is connected there.
Poorly washed dirt from the dishes. Everything may turn out to be quite banal - for example, you have purchased low-quality detergent, or, for example, you forgot to pour rinse aid into the dispenser. Or maybe the situation is much worse - either a clogging of the internal cavity of the machine, or a general imbalance of parts is possible. In this case, buying a new detergent can not do: you have to call the master.
Programs are not executing correctly. If you installed the program manually, check the settings. If the program is automatically selected, there may be two options: either the electronics failed, or the heating element of the machine is damaged - in both cases, again, you will have to call the wizard.
During operation of the dishwasher, the consumption of electricity increases sharply (or even knocks plugs). Most likely, the heater (heating element) is out of order and its replacement is necessary.
Water does not heat up. Most likely, the heater failed,
Water leaks under the dishwasher. Perhaps there is a hole somewhere in the pipes or hoses. Another option: the water collection hopper burst.
Some strange extraneous sounds are heard. There can be two options: a) wear of the stuffing box - in this case, water enters the bearing, it makes such sounds, b) the pump is worn out
Water overflows continuously. To start, look: the dishwasher is turned on or off. If it’s turned on, it means that the matter is in the water level sensors, if it is turned off, it means that the solenoid valve for filling the water is faulty.
No water pressure. Again, two options are possible: either the nozzles are clogged or the supercharger is faulty.
The dishwasher does not turn on at all. To get started, try a different outlet. Did not help? So, the matter is either a malfunction of the network button, or a surge protector, or a door lock device.
What keys do we use ?:
buy a dishwasher bosch
hansa dishwasher
bosch dishwasher 45 cm
dishwasher video
instructions + for dishwashers
So, one fine day, you find that the dishwasher does not turn on, does not drain water or leaks. Do not rush to immediately call the master, because sometimes the cause of the breakdown can easily be eliminated with your own hands without special skills and tools. Next, we will consider possible malfunctions of dishwashers and instructions for their independent repair at home.
What could cause a failure?
If the equipment has served you for more than 5 years, and its warranty has long expired, it means that the banal wear of spare parts may be a possible cause of the malfunction.
In the event that you have recently made a purchase and the dishwasher is already out of order, then the causes of failure can be as follows:
- Poor assembly and spare parts themselves. It is found in cheap Chinese models from poorly known manufacturers.
- Before loading the dishes into the chamber, you do not wash away the remnants of food that clog the filter. Very dirty dishes most of the dishwashers do not completely rinse, as a result of which you have to rinse additionally manually.
- Outlet malfunction. A banal situation but still sometimes arises.
- Incorrect connection of the dishwasher (for example, the drain hose is longer than the permissible value or the cold water hose is loose).
- A poor detergent that does not wash dishes well or does not wash dishes at all.
- Perhaps you just tightly closed the door (the mechanism is designed so that the equipment does not turn on until the latches work). It should be noted right away that on some models the door does not lock in the lower position. If the door does not hold it is not a dishwasher breakdown, but a manufacturer’s defect.
- Another fairly popular cause of the malfunction is improper loading of dishes, as a result of which the appliance does not wash the lower section or the upper shelf badly. Even in the instructions, the correct load is discussed - the top needs to be filled with plates and mugs, the bottom - with overall kitchen utensils (for example, pots). Another important requirement - glasses and cups should be stacked upside down.
If not one of these reasons is the culprit of the failure, then the matter is in the spare parts, which we will talk about later.
Troubleshooting common types of problems
The dishwashing process does not start
Such a situation: you turned on a certain mode, all indicators light up, the sound of filling the water is heard from the camera, it has warmed up, but the washing process itself does not occur. In this case, the likely causes of damage to the dishwasher may be:
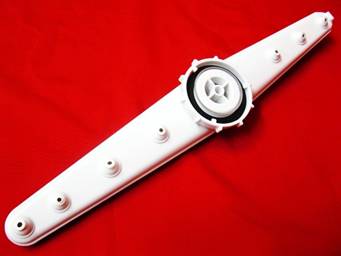
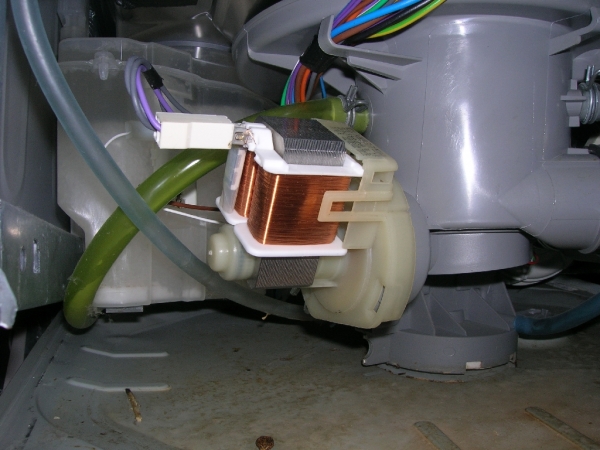
The failure of the circulation pump can be determined by the characteristic sound of its operation. If there is no noise after filling the water, most likely the reason is in it! As you can see, replacing is not a big deal.
Dishwasher pump repair workshop
It should also be noted that a possible malfunction of the dishwasher may be damage to the electric motor, or rather its winding. To make sure that the engine is working, check it with a multimeter for an interturn circuit and an open circuit.
Water overflows
Most likely, the water level sensor has broken. It is located at the very bottom of the equipment, so for access it will be necessary to turn the dishwasher, and then replace the sensor with a new one.
We draw your attention to the fact that if the unit is turned off and water is being poured into the chamber, then this is not a sensor, but an electromagnetic valve, which should shut off the fluid supply. Replacing the valve is straightforward.
Overheating / underheating of water
It also happens that the dishwasher overheats or vice versa does not heat the water. In the first case, the temperature sensor breaks, which entails overheating of the water, the formation of a large volume of steam and the shutdown of the equipment.
As for underheating, there can be several causes of the malfunction:
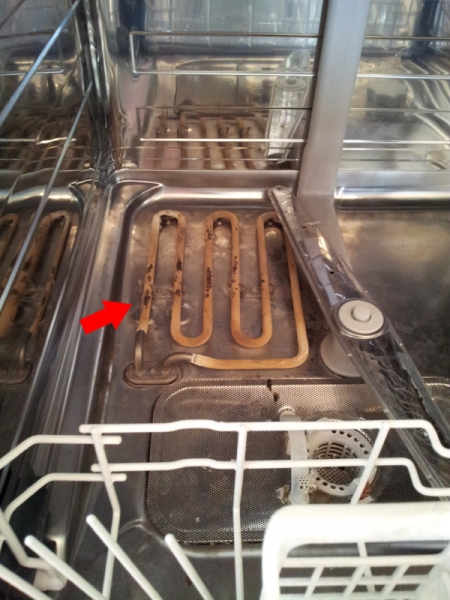
There is no discharge
If, after washing, the water does not drain into the sewer, then the pump may be broken or the drainage system clogged, as a result of which the dishwasher does not drain the water.
As for the first case, you need to check the drain pump for debris and winding resistance. Most likely, the water is in the dishwasher because the pump just clogged, although sometimes the start-up may not occur even because of the pressure of the water. If the pump is in order, check the entire drainage system, including the siphon. Most likely, the hose is clogged, which just needs to be cleaned or the filter inside the camera.
There is another frequent case when the dishwasher does not completely drain the water. Here, most likely you pulled up the drain hose too much and after draining (when the pump shuts down), part of the water returns back to the chamber.
The case is beating current
If the dishwasher is shocking, then with a probability of 99% it can be argued that the heating element - TEN - is broken. All you need to do is to open access to the heater and visually inspect it for cracks and other types of defects. If the heating element is really damaged, replace it with a new one.
The reason why the heater fails is the poor quality of the water (too hard). Also, one more malfunction may be the failure of the heater relay. The instructions for replacing the parts were clearly demonstrated in the video:
Change the relay on the control module
Does not pick up detergent
If you notice that the dishwasher does not pick up the powder or the tablet, the cause of the breakage is most likely the contamination of the nozzles or the weak pressure of the water, as a result of which it does not enter the dispenser. A possible cause may be a breakdown of the valve opening mechanism, from which the detergent is washed. If the valve does not open the water intake (or closes poorly), the tablet may not completely dissolve, as a result of which the appliance does not wash the dishes well.
Lack of power
If you notice that the time indicator does not even light up or the appliance does not respond to the press of a button, then the causes of a dishwasher malfunction can be as follows:
- broken outlet;
- the door latch did not work, or the lock device burned out;
- the network button does not work;
- surge protector does not work.
In all cases, you need to use a multimeter to check all the elements of the electrical circuit and find out why the dishwasher does not turn on with the exception method. If in your case the dishwasher does not end the cycle or you cannot switch the program, check the programmer and the control unit, most likely the modes do not work due to its malfunction.
Extraneous noise
Extraneous noise indicates that the bearings of the pump or electric motor (supercharger) have been damaged. The bearings break due to the ingress of water, which in turn seeps through the damaged seal. Bottom line - the dishwasher is buzzing at work. In this case, you will need not only to replace the bearing, but also the gland itself, otherwise the same problem will arise again after a while. By the way, another reason for extraneous noise may be associated with the pump - garbage has fallen into the area of \u200b\u200bthe sprayer or impeller. Everything is simple here, remove the trash and check the impeller for defects (the blades may have already been damaged, which causes noise).
Dishes do not dry
Some modern models feature a function for drying washed dishes. This process occurs when the fan is installed inside the camera. If you find that the dishwasher does not dry the dishes (or does not dry out), but otherwise functions normally, the fan most likely broke. All you need is to check its winding, as well as the supply contacts with a multimeter, and if there is a need, replace the spare part with a new one. We talked about how to use a multimeter in the corresponding article.
Water leaks on the floor
Well, the last one of the most popular breakdowns of the dishwasher is the leakage of water to the floor under the body.
There are four main causes of leaks:
- Door seals in unsatisfactory condition, as a result of which the door is not tightly closed. They must either be changed, or if possible, cleaned from plaque.
- The pump seal that pumps water is damaged. Best replaced with a new one.
- The clamps on the drain and water supply hose are loosely tightened, resulting in leakage. Seals may also not be installed at the junction points.
- Damaged water tank located on the side of the equipment. Most often, the tank cannot be repaired, so it is replaced by a whole one.
To correctly determine the place of water seepage, it is recommended to remove the equipment cover and put newspaper sheets on the floor. Where the newspaper gets wet and there will be a breakdown.
Video leak repair tutorial
That is all the main malfunctions of dishwashers. We hope that now you can repair the equipment yourself if it stops working, starts to make noise or does not drain the water after washing the dishes.
Video filter cleaning instructions
Change the relay on the control module
Dishwasher pump repair workshop
Video leak repair tutorial
A dishwasher in the kitchen is a luxury that you quickly get used to and do not want to refuse. What if it no longer works or works poorly? Consider the possible causes of failures and how to resolve them. Also in the article you will find fault codes of most popular brands of cars.
On the Russian market, you can now purchase more than 130 models of dishwashers, which are structurally different even within the range of one manufacturer. In this regard, there are both malfunctions that can occur with various units, and individual "thin spots" in individual models. In one article it is impossible to cover all cases and models, so we made a selection of frequently occurring breakdowns.
Attention! Before starting work, close the water tap and unplug the machine. Examine the basic machine error codes, design, and diagrams that are in the documentation.
Simple repair that does not require professional skills
Consider the problems that can be fixed without the involvement of specialists. Almost all of them have the root cause of blockages of various nodes. The blockage is external and internal.
Elimination of external blockages
The cause of the external blockage may be in the drain. If the water at all drain points leaves with a noticeable difficulty, then this problem must be solved by mechanical or chemical cleaning of the siphon and sewer pipes. Clogging can occur in hoses. They can be twisted, twisted, pinched - in this case they need to be straightened. If they are covered with limescale from hard water - you need to disconnect them from the machine and clean.
Proper drain connection
Elimination of internal blockages
Internal blockage focuses:
- in the internal filter - due to abundant food debris on the dishes;
- in the water drainage system - due to small food debris that has passed through the filter;
- in the intake valve filter - due to hard water;
- in the drain pump - due to solid, insoluble particles of debris entering directly into the pump;
- in the blades (rocker arms) - due to food debris and scale.
Removing the internal filter
If the car stopped with water inside, you need to click on "Drain" and wait for the camera to empty and disconnect the unit from the network. The remaining water must be removed with a sponge. Do not clean the dirt with your bare hands unless you are sure that there are no glass fragments in the mass of contamination.
Since the arrangement of elements differs in different designs, it is necessary to study the operating instructions (service book, passport). Locate the attachment points of filters or other assemblies, and, armed with a screwdriver, tweezers, a wrench, pliers or other suitable tool, get to the clogged part, remove it and clean and rinse it well, and then reinstall it.
Video about replacing filters using the Hotpoint dishwasher as an example
When using a detergent with a high foaming coefficient, water can get into the pan, which will lead to the inclusion of “aquastop”. Water must be removed from the sump. If you can’t get to it yourself, just don’t use the machine for a while: the water will dry and the machine will work normally.
Checking electrical contacts
If the engine does not start, check the fuse and switch on the electrical panel, as well as the integrity of the wiring. When replacing a fuse, it is necessary to choose a part similar to that to be removed.
If this is not the problem, you need to evaluate the condition of the contacts in the junction box, which is usually located under the protective shield. Power to the machine is supplied through the clamps, which can fail due to vibration and moisture. The reason for the lack of power may be in the terminal box. The contacts must be cleaned of rust with sandpaper and the clamps in place.
The engine may not turn on if the door is closed incorrectly or the latch does not work.
Lack of water supply may result from failure of the supply valve. It is necessary to disconnect and remove it, and then measure the resistance. If it does not correspond to the passport certificate, then an open or short circuit has occurred and the valve needs to be replaced.
If you hear the sound of a running engine, but no water enters the chamber, the drive belt may be damaged.
Other easy fixes
Another simple repair is replacing worn or damaged gaskets, pipes and hoses located outside the dishwasher. In the event of a leak, first of all, it is necessary to inspect the external inlets and outlets of water, and, if a violation of their integrity is detected, replace them with new ones.
If you find that water is flowing from under the door of the dishwasher, then a possible problem is the wear of the seal. The profile seal is easy to remove and install.
If there is knocking (ringing) from the machine, the dishes may have been installed incorrectly, and during rotation the sprayer clings to its edges. Always check that the dishes are in the correct position - with the cavity down and all parts above the basket. It is also easy to replace the spray nozzle.
If the sprinkler mount is cracked, the upper mounting nut is loose, or the seal is worn, they can be easily replaced. How to remove and replace the sprinkler elements (upper and lower) is described in the video.
If the lid of the detergent dispenser seizes during loading or operation, it must be replaced. A possible malfunction also concerns the drive between the dispenser and the wax engine (on some models). It may be necessary to replace the drive or the dispenser assembly.
If any of the rollers on which the basket extends is damaged, this will interfere with the normal loading and unloading of the machine.
Medium Repair
The video below shows the process of replacing a turbidity valve. The video is also useful in that it examines in detail the dismantling of the machine from the installation site and its extension from the niche for further manipulations.
Medium complexity repairs include troubleshooting the door elements of the dishwasher.
If the machine cannot function normally due to a broken door lock, it must be repaired, and in some cases replaced. In order to get to the door lock, you have to disassemble the front panel. On how to replace the door lock mechanism, see the video.
If your dishwasher is decorated with the same facade as the rest of the kitchen furniture, the door cables may not support the extra weight and break. The following video tells about their replacement.
If the door hardly opens or closes, there may be a problem with the hinges. On how to replace the hinge or spring of the loop, see the video.
A malfunction may affect the water filling system. Structurally, the system can be different and operate on parameters: pressure, time or flow. In the filling system, which is triggered by pressure, a diaphragm is installed that closes the contactor. Over time, due to hard water, impurities and calcareous deposits, the diaphragm loses its ability to close the contactor and it is necessary to clean or replace this element.
The system based on a reed switch (meter, flow meter) is very sensitive to an increase in water pressure in the line and may issue incorrect filling commands. When the error code "system failure" is issued, it is necessary to replace the sensor, and when the blades are jammed, only repair in the service center or replacement of the unit will help.
Complicated repairs
Repairs requiring significant intervention in the design of the machine are considered complex. In order to do everything right, you need to carefully study the device of your model of the dishwasher and have the skills of self-repair of household appliances. If you are not sure that, having disassembled the structure, you will assemble it correctly, it is better to call a specialist from the service center.
Replacing the dishwasher motor and pump
The fact that the engine or pump is no longer working as needed due to complete wear and tear, you will be informed of alarming symptoms: leaks, screeching sounds, violation of water splashing (the dishes remain dirty). In this case, replace the engine / pump assembly with a new one. To do this, dismantle the bottom panel. How to accomplish this is described in the videos.
Procedure for Hotpoint Machines
Procedure for Whirlpool machines
Control Module Replacement
To determine the malfunction of the control module, a complete diagnosis of the system is required, performed on special equipment. Moreover, repairing the module yourself is not worth it, but you can replace the failed module with your own hands. To do this, the door of the dishwasher is partially disassembled and the control panel is removed, then the sensor of the unit and the electric wire are disconnected. The new control module is connected in the reverse order. The process is illustrated in the video.
Another serious problem may be the failure of the heating system of the dishwasher. Water does not heat up or does not heat up enough. About how to replace the relay, TENA look at the video.
Error Codes
Machines equipped with a self-diagnostic function report a problem with an error code that appears on the display in the form of numbers or a combination of light signals on the panel. Each manufacturer has its own encoding, which should be listed in the passport or operating instructions of the unit. Not all manufacturers indicate the causes and methods of troubleshooting, but for the owners of some models we have such information.
Table 1. Cars Bosch, Siemens, Neff, Gaggenau
The code | Causes of occurrence | |
E1 | Heating error |
Most often, this is a malfunction of the heating element - there is no resistance or leakage to the housing. The element on the electronic module responsible for the operation of the heater is defective. Check safety thermostat. Check flow sensor. Check the pressure switch (water level sensor). |
E2 | NTC sensor error (temperature sensor) |
Defective NTC sensor, which feeds information to the PM control unit. As a rule, it is located in a block with a heating element and has a certain resistance (~ 55 kOhm at 21 ° C). |
E3 | Water filling problems | If the desired water level has not been reached within a certain amount of time. Depending on the model of the dishwasher (PM), the sequence of actions will be different. Either the PM will wait until the filling is completed (earlier models), or the water will be drained within one minute (later models). Faulty Aquastop hose. Defective water drain pump. Check inlet valve. Inlet filter clogged. Faulty pressure switch. |
E4 | Flow Switch Issues | The water flow switch is not at the set position. He is responsible for the distribution of water in the sprinklers and is installed under the heating element. Clogged switch. A malfunction of the engine that acts on the flow switch and sets it to one or another position. |
E5 | Exceeding fill level |
The pressure switch tube is clogged. Defective pressure switch (water level switch). Inlet valve defective. |
E6 | Aquasensor Error | An aquasensor is an element that controls the turbidity, hardness, and contamination of water during rinsing at the initial stage. If the dishes are slightly contaminated, it helps to eliminate rinsing and saves water and energy. Located next to the heater. |
E8 | Low pan level | The heating element does not turn on. The circulation pump does not have enough water pressure and a pulse is applied to the module. Check water head. |
E9 | TEN error | Most often occurs in dishwashers with a flow heater, which is built into the circulation pump, when the heating element breaks. Check the heater for an open. |
E11 | PMM works without a heater | Check NTC sensor, electronic module, power wires. |
E14 | Flow sensor error | The flow sensor does not detect control pulses, while they flow to the circulation pump. |
E15 | Aquastop worked | A water leak has occurred. Check the water in the pan. The causes of leaks may vary. |
E16 | Unauthorized collection of water | Check inlet valve (flow sensor). Check the pressure switch (level sensor). One option is increased foaming. |
E17 | Water Gulf Error | Check flow sensor. Inlet pressure may also be too high. |
E18 | Do not turn off the power. The program will end after draining the water. | |
E21 | Problems with the drain pump | The drain pump is blocked. Check the impeller of the pump for a foreign object. If there is no blockage, then the pump is probably worn out and sometimes can jam during rotation - it must be replaced. |
E24 | Water drain error | The hose for draining dirty water is pinched or broken. |
E27 | Mains undervoltage | Check the voltage at the outlet. The error more often appears during peak hours on urban power grids. As an option - put a voltage regulator. |
Table 2. Cars Electrolux, Zanussi, AEG
The code | Causes of occurrence | LED signal END | Checking and troubleshooting |
i10 | No water | 1 blink | Within 60 seconds, the threshold level for switching the water level switch (pressure switch) has not been reached. the water tap is blocked or closed; clogged filter in the inlet hose; the inlet hose is pinched or bent. |
i20 | Does not drain water | 2 blinks | The water level switch did not work within the set drain period. clogged drain system; the drain hose is pinched or pinched; faulty level switch (pressure switch). |
i30 | Overfill protection system has worked | 3 blinks | There was a leak, water collected in the bottom of the body |
i50 | Circuit pump triac short circuit | 5 flashes | The circulation pump starts to run at uncontrolled, maximum speeds, after which the washing is interrupted. A replacement triac on the control board is required. |
i60 | No water heating or overheating | 6 blinks |
heating element defective; safety thermostat tripped; faulty wiring; faulty temperature sensor; insufficient level of water circulating in the machine; circulation pump defective; faulty control board. |
i70 | Open or short circuit NTC thermistor | 7 flashes | The program runs to the end without using the heating function. |
i80 | Error communicating with external EEPROM | 8 blinks | No communication with EEPROM flash memory. |
i90 | Incorrect checksum (programming model) MCF or CCF | 9 flashes | Program selection is not possible. The ON / OFF LED lights up. |
iA0 | Sprinkler blocked | 10 flashes | At the beginning of the program and each subprogram, as well as after opening / closing the door or interruptions in energy supply, the rotation of the sprayer is checked and evaluated. |
ib0 | Transparency sensor defective | 11 flashes | The water transparency signal required for calibration was not received within 15 seconds. The definition of transparency always happens. According to this indication, the program route is adapted. |
iC0 | Lost user interface | 12 flashes | The machine stops and waits until communication is restored. |
id0 | No signal from tachogenerator | 13 flashes | The circulation pump is turned on, but the signal from the tachogenerator is not received within 20 seconds. The circulation pump is uncontrollable, the heating is off. This function is checked again at each stage of the program. |
iF0 | Water fill time error | 14 flashes | Time limit exceeded when filling with water. The program runs until the next subprogram when the water level is insufficient. Further flooding to the required level does not occur. The error disappears after the discharge. |
Table 3. Machines Hotpoint-Ariston, Indesit (with display)
The code | Description |
A01 | The Leakage Protection System (Aquastop) has worked - the dishwasher will drain until it is turned off. Check pressure regulator. Check wiring. |
A02 | The dishwasher does not heat water. Check wiring. Check pressure sensor. |
A03 | Thermistor error detected. Check wiring for thermistor. Check the thermistor. |
A04 | Check the water heater. Check thermostats or thermistors. Check wiring. Check pressure sensor. Check the safety thermostat. Check heater relay on control panel. |
A05 | The water level switch or level sensor does not reset three minutes twenty seconds after the drain starts. Check the filters. Check the blockage of the drain pump. Check the drain pump. Check switch or level sensor. |
A06 | Check the water supply. Check inlet hose. Check wiring. |
A07 | An error was detected in the triac of the auxiliary water pump. Check the drain pump. Check if AQUASTOP leak protection is enabled. |
A08 | Water pump triac error. Check the circulation pump lock. Check the control panel. |
A09 | A malfunction of the main water pump has been detected. Check the filters. Check the circulation pump motor lock. Check the main circulation pump. |
A10 | A fault has been detected in the triac solenoid. Check the water inlet valve. Check wiring. Check the control panel. |
A11 | Insufficient triac load. Check relay valve. Check pump. Check the control panel. |
A12 | Heater relay open. Check the water heater. Check thermostats or thermistors. Check wiring. Check heater relay on control panel. |
A13 | Detergents, dispenser error. Check the soap or tablet dispenser solenoid. Check wiring. |
H2O | There is no water or a small pressure of water. Check the water supply. Check inlet hose. Check the water inlet valve. Check wiring. |
Table 4. Ariston, Indesit machines (indicators, without display)
4 programs | 6 programs | Description |
Aquastop | ||
Door lock | ||
TEN | ||
NTC in the cliff | ||
TEN | ||
No drain | ||
Low water pressure | ||
Motor blocked | ||
Memory firmware required | ||
Flash card firmware required |
Table 5. Machines Asko, DW20.1, DW20.2, DW20.3, DW20.4, DW20.5, DW20.C
LEDs | Display | Problem | Solutions |
L1 | F1 | Heating problem (no indication in DW20.1) A temperature increase of less than 5 ° C for ten minutes. The program exits the heating stage and continues the washing process. Indication only in the service menu. |
Check: thermistor, water level, circulation pump and control unit, wiring. |
L2 | F2 | Overflow Too much water in the machine (pressure sensor) or the float is activated. If the water is not drained within 60 seconds, the program will be interrupted (the drain pump is switched on). |
Check: drain pump (clogged hoses), flow sensor, intake valve, leaks, wiring. |
L3 | F3 | The problem with the thermistor, the so-called. temperature sensor (no indication in DW20.1) Discontinuation or\u003e 80 ° C. The program exits the heating stage and continues the washing process. Indication only in the service menu. |
Check: thermistor, control unit. |
L4 | F4 | Water intake problem (no indication in DW20.1) <80 импульсов в течение 60 секунд или не достигнуто правильное количество импульсов в течение 255 секунд. Программа прерывается. |
Check: water supply, flow sensor, intake valve, wiring. |
L11 | F5 | Valve leakage (no indication in DW20.1) \u003e 80 recorded pulses, then the intake valve shuts off. Any program in progress is interrupted (drain pump activated). |
Check: leak through inlet valve, flow sensor. |
L12 | F6 | Pressure sensor malfunction Output signal\u003e 4.8 V. The program continues. Indication only in the service menu. |
Check: pressure sensor, control unit and wiring. |
L1 + L2 | F7 | Water does not drain (machines with pressure sensor) Water does not drain after 120 seconds of pumping. The program is interrupted. |
Check: drain pump, hoses, drain hose installation, control unit and wiring. |
L1 + L3 | F8 | Filter clogging The pressure sensor senses excessively low pressure during the last rinse. Indication after completion of the program. |
Check: filter, crankcase (pressure chamber), pressure sensor. |
L1 + L4 | F9 | Circulation problem The pressure sensor senses an excessively low pressure (for example, there is no water in the machine) or an excessively high pressure (for example, the circulation pump is faulty). The program exits the heating stage and continues the process. Indication only in the service menu. |
Check: circulation pump, filter, water level, pressure chamber and pressure sensor. |
L1 + L11 | FA | Turbidity Sensor Problem Indication only on the service menu. The machine determines the high turbidity for “path selection” in the automatic program. |
Check: water quality, turbidity sensor filter, drain system. |
L1 + L12 | Fb | Spray problems Contacts are constantly closed or open. The program continues. Indication only on the service menu. |
Check: sprayer (function of gearbox, contacts and wires). |
L7 | Salt Indicator (DW 20.5) | ||
L6 | Rinse aid indicator (DW 20.5) | ||
L7 | The door is open | ||
L7 | The door is closed |
Table 6. GORENJE machines (with display)
Table 7. GORENJE machines (with LED panel)
Model | Error code | Lamp combination | Cause | Verify |
For models of 45/60 cm on which control modules with a part are installed the numbers (220003513/220004987/220003355) | E1 | The sensor for leaks and the presence of water in the pan (if installed) has triggered. | ||
E2 | Water overflow sensor has triggered. | |||
E3 | No heating water. |
|
||
E4 | Open temperature sensor. |
|
||
E5 | No gulf of water. | Chains, devices, water inlet / outlet channels, Aquastop. | ||
E6 | No drain. | Chains, devices, water inlet / outlet channels, Aquastop. | ||
E9 | See error E9 |
Table 8. Miele Machines
The code | Causes | Checking and troubleshooting |
F01 | NTC temperature sensor short circuit | NTC temperature sensor (R30) or its connecting wires in short circuit. check the NTC sensor; check connectors. |
F02 | NTC temperature sensor open | After an error occurs, the heating will be turned off. NTC temperature sensor (R30) or its connecting wires are open. check the NTC sensor; check connectors. |
F11 | Water does not drain | Water does not drain from the dishwasher. clogged drain system; clogged filters; the drain pump is faulty; malfunctioning water pressure switch of the heating element. |
F12 | Water does not enter the machine initially |
Water tap shut off. Inlet valve defective. An open in the power circuit of the water flow sensor. |
F13 | Water does not flow: heater pressure switch error | Water tap shut off. Inlet valve defective. Defective water flow sensor. Insufficient water pressure in the water supply system. Inlet valve filter clogged. |
F14 | Heater pressure switch error | The program is interrupted and the drain pump starts. Heater pressure switch defective (check pressure switch, check wiring). Low pressure of the circulation pump (check the condenser, check the pump itself). Defective water flow sensor. |
Table 9. Whirlpool Machines
The code | E - flashing LED F - flash |
Causes of occurrence | Checking and troubleshooting |
E1 | 1-5 | Aquastop worked | Check the circuits, devices, nozzles, drain / fill water channels. |
E2 | 2-5 | Security concerns | Check circuits, devices, channels. |
E3 | 1-2-5 | Heating error | Heating control circuits, devices responsible for heating. |
E4 | 3-5 | Temperature Sensor Failure | Short circuit or other defect. |
E5 | 1-3-5 | Water problem | The increased time of a gulf of water. Check inlet valve, akvastop hose for water supply, pressure switch. |
E6 | 2-3-5 | Water does not drain | Check pump, water drain hoses, connections. |
F0 | 10 | Sensor damage | It will be shown only in the test program. |
F1 | 1 | NTC sensor defective | Temperature outside normal range (-3 ° C to +85 ° C). The temperature inside is higher than +85 ° C. Bad NTC is the most common cause of this error. |
F2 | 2 | Water leak | Water is in the lower tray. A float or float switch turns off the water inlet valve and the drain pump is turned on until the pressure sensor indicates that the tank is empty. There are many reasons for this error, but it usually comes down to leakage. |
F3 | 3 | Heating system error | Appears after about 25 minutes of not reaching operating temperature. Heating is too slow (less than 1.5 ° C for 10 min). the water heater or heating element is faulty (this is the most common reason); faulty relay (RE2) on the control board (CB); nTC defective. |
F4 | 4 | No draining water | The drain pump starts to turn on, but after 4 minutes, the machine detects that the tank is "not empty." defective or blocked drain pump; clogged drain system; faulty control board. |
F5 | 5 | Sprinkler blocked | Check the water spray. |
F6 | 6 | No water | The inlet valve is on, but the flow meter is not sending pulses and the water indicator is off. the water tap is closed; water blockage; inlet valve defective; defective flow sensor. |
F7 | 7 | Water Flow Sensor Error | The inlet valve turns on, the water indicator is on. the water flow sensor sends too weak pulses; the water tap is closed; water blockage; inlet valve defective; defective flow sensor. |
F8 | 8 | Low water level | The mechanical water level indicator WI has tripped. The optical OWI water indicator has been activated. internal filters are dirty; strong foaming occurred, accompanied by a decrease in water volume; sprinkler is unstable. |
F9 | 9 | Continuous water supply | The inlet valve is turned off, but it is not mechanically closed and passes water into the machine. inlet valve defective (mechanical damage); the control board is faulty (short circuit of the system). |
FA | 11 | OWI Optical Water Indicator Error |
oWI indicator is faulty; oWI lens contamination; faulty control board; check power wires. |
FC | 13 | Water hardness sensor error | Faulty water hardness sensor. |
Table 10. LG machines
The code | Error description | Causes of error |
IE | Water does not enter the tank Water did not reach the first level in the allotted time (4 minutes). |
There is no water in the piping. Low water pressure. Faulty water inlet valve. Faulty water level switch (pressure switch). |
PE | Error of the water level sensor (pressure switch) An error code is displayed if, for a certain time, the tank was not filled with water to the nominal level (after 25 minutes) or if the water was filled faster than the allotted time (4 minutes). |
Defective water level sensor. Unacceptably low or too high water pressure in the water supply. |
FE | Tank overflow An error code is displayed if the maximum water level in the tank has been reached. |
The causes of the error can be caused by defects in the electronic controller, level sensor or water inlet valve. |
OE | No water drain An error occurs if, after 5 minutes after the start of the drain pump, the water has not been drained from the tank. |
The drainage path is blocked (drainage system). Faulty electronic controller. Defective drain pump. The water level sensor is out of order. |
tE | Invalid water temperature |
An error occurs if the temperature sensor in the CM is faulty (open or short circuit). |
LE | Lock error |
In most cases, this error is caused by a low voltage in the mains. It is also necessary to check the serviceability of the electronic controller and drive motor. |
Ae | Auto power off error | no information |
E1 | Water leaking into the pan |
There was a leak of water into the pan due to depressurization of the tank, hoses or other components of the CM. Faulty water leakage sensor. |
HE | Faulty water heating heater |
Check the heater and its supply circuit. |
Table 11. Ardo Machines
The code | Error description | Causes of error |
E1 | The aquastop water leakage protection system has turned on. | Check the hoses and their attachment to the dishwasher. |
E3 | The machine automatically overfilled the water and turned on the safety level. | - |
E4 | There is no way to heat the water. | The temperature sensor may be defective or its readings are erroneous. |
E5 | There is no water in the cooking chamber. | The feed valve may be closed or the inlet hose may be disconnected. |
E6 | No water drain | Problems in connecting the drain hose, malfunctions in the drain pump. |
Table 12. Samsung Machines
The code | Description |
E1 | Exceeded the time of water supply or its limitation, low pressure. It is necessary to check the presence of cold water and the pressure in the water supply. |
E2 | Drain failure. Water does not drain completely, or an error has occurred in the operation of the water level sensor. Check if the drain is clogged with food debris, clean it if necessary. |
E3 | The increase in the operating time of the heating elements, obtaining the optimum water temperature does not occur. |
E4 | Water leakage or overflow. Water leakage, or excessive water supply. The likely cause of the occurrence is a malfunction of the bay valve or water level sensor. |
E5 | Weak pressure of water. Insufficient water level in the dishwasher or malfunction of the delivery level sensor. |
E6 | Temperature sensor malfunction. Breakage or short circuit. |
E7 | Violation of the temperature sensor. Sensor malfunction or open. |
E8 | Alternate valve operation error. It is not possible to set the FLEX function valve to the desired position. |
E9 | Button defect. If you hold the button for more than 30 seconds. A possible cause of the problem is a short circuit, or a button is stuck. |
EA | Violation of the water level sensor. Excess water in the dishwasher or problems with switching the water pressure. Check the position of the drain hose, at the end of the washing cycle, clean the drain from food residues. |
UC | Voltage problems. Electricity is supplied in the range of less than 180 V or more than 270 V. To avoid a short circuit or breakdown of the machine, it is recommended to reset the washing program and wait for a stable voltage in the mains. |
Table 13. Beko Machines
The code | Error description | Causes of error |
H1 | Faulty temperature sensor | Measure the resistance of the temperature sensor. It is about 4700 ohms at an ambient temperature. environment +25 ° С. |
H2 | Defective heater (heater) |
Disconnect one of the TEN plugs and measure its resistance. It should be 20-30 ohms. Replace the heater. Replace electronic controller. |
H3 | TEN is constantly switched on, constant heating. |
Measure the resistance of the temperature sensor (plug J2). It is approximately 4700 Ohms at an ambient temperature of +25 ° C. Replace electronic board. |
H4 | The triac of the water inlet valve is closed. | After checking the wires and connections, replace the electronic board. |
H5 | The drain pump is faulty, the pump is closed, not connected. |
Check and clean the pump filter. The drain hose should be between 60 cm and 1 m above the floor. Check the drain hose, it should not be damaged or kinked. |
H6 | Faulty motor triac |
Replace triac. Replace module. Replace engine. |
H7 | Water Level Sensor Error |
Check door washing machine (must be closed). Check the water tap. Check the connections between the water level sensor and the electronic board. Replace water level sensor. Is 220 V applied to the valve? Also check the voltage at J3 and J4. Replace filler valve. Replace electronic module. |
Table 14. Candy Machines
The code | Error description | Verify |
E1 | Water fill error, the “full tank” signal was not reached in 4.30 minutes after the start of the bay. |
Chains, devices, water inlet / outlet channels, Aquastop. |
E2 | Drain error, the “empty tank” signal is not reached 4 minutes after the start of the drain. |
Chains, devices, water inlet / outlet channels, Aquastop. |
E3 | Failure to reach the set water temperature for the wash cycle. |
Heating element. Heating control circuits, devices responsible for heating. |
E4 | The anti-leak system worked. Water in the pan. |
Chains, devices, water inlet / outlet channels, Aquastop. |
E5 | The NTC temperature sensor is open or shorted. |
Sensor defective / open. Open in connectors / wires. Temperature< -5 °C |
Table 15. Kaiser Machines
The code | Cause | Verify |
E1 | Extended bay time. | |
E2 | Extended drain time. | Chains, devices, water inlet / outlet channels, Aquastop |
E3 | Extended warm-up time. |
Heating element. Heating control circuits, devices responsible for heating. |
E4 | Overflow. | Chains, devices, water inlet / outlet channels, Aquastop |
E5 | Failure of the temperature sensor "The temperature sensor is open, short circuit or other defect." |
Heating element. Heating control circuits, devices responsible for heating. |
E6 | The temperature sensor circuit is broken. Connect the temperature sensor. |
Heating element. Heating control circuits, devices responsible for heating. |
E7 | Short circuit of the temperature sensor. Check the temperature sensor circuit. |
Heating element. Heating control circuits, devices responsible for heating. |
Table 16. Kueppersbusch machines
Table 17. KRONA Machines
Table 18. Fagor Machines
The code | Description |
F1 | Drain error, aquastop turned on to prevent leakage. |
F2 | Error determining the water level in the working chamber. |
F3 | Faulty temperature sensors. |
F4 | Malfunction in a chain of temperature sensors. |
F5 | Water is not filled or is produced incorrectly. |
F6 | Water is not drained or is not performed correctly. |
F7 | Malfunction of the turbine (where it is), or a malfunction of the water level sensor. |
F8 | The alternate washing mode does not work. |
F9 | The water filling system is technically incorrect. |
F0 | The control controller board may be malfunctioning. |
A dishwasher is not such a complicated technique as it seems at first glance. Most failures are caused by simple causes. To eliminate them, you do not need high qualifications or special knowledge. If the equipment is no longer under warranty, you can completely try to repair it yourself. The main malfunctions of dishwashers and methods for their elimination will be described further. In most cases, the causes and methods of elimination are independent of the make of the machine. Bosch, Siemens, Sumsung, Electrolux, Miele, Indesit, Candy, Beko - it does not matter. Repair is the same. Disassembly process, mounting, etc. may vary. But the basic principles of finding the causes and troubleshooting of dishwashers are the same.
Dishwasher is the dream of any housewife
To repair a dishwasher, it is necessary to represent the processes that occur in it. This is the only way to determine the possible causes of failure and eliminate them as soon as possible.
We describe the general principle of the functioning of the dishwasher. The operation algorithm is usually the same for all manufacturers, although some changes may occur. Next, we describe the longest process in time - washing dirty dishes with time to “acidify” the remaining food.
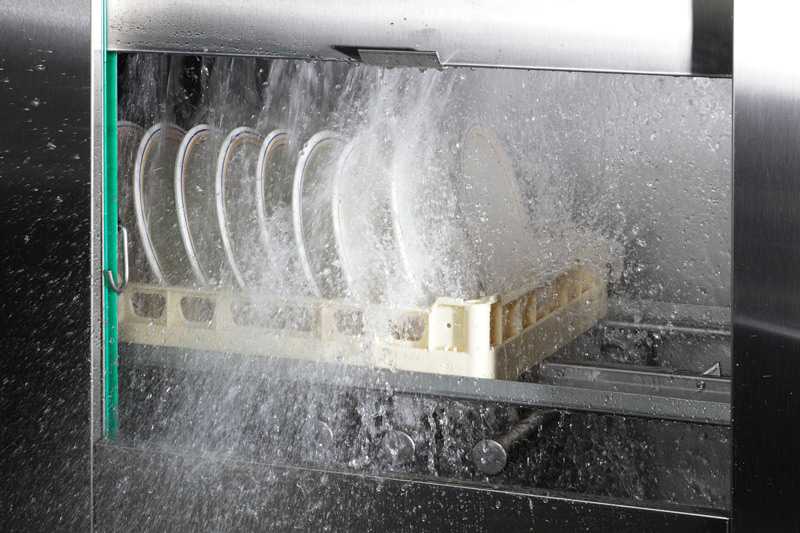
As you can see, a large number of sensors are involved in the process. All of them can fail and cause damage. Filters, nozzles, sprinklers may also clog. All this is the cause of the breakdown.
Breakdowns, possible causes, elimination
Many breakdowns of the dishwasher are repaired by simple steps. Often problems are associated with low voltage in the mains or low pressure in the water supply. A lot of breakdowns are explained by the fact that the leftovers of food clog filters, grates, holes. All these reasons can be eliminated on your own, returning to working capacity.
The dishwasher does not collect or drain water - you can figure out the reasons yourself
We check at the very beginning and if the PM does not start working
Many malfunctions of dishwashers are explained by simple reasons - a voltage drop in the network, insufficient water pressure, clogged filters, etc. At the very beginning, after we find that the dishwasher does not work or works with deviations, we check:
These are very simple steps, but it is for these reasons that the dishwasher often does not start up.
Water leak
Some dishwasher problems are caused by water leakage. Then the dishwasher stops during operation and no longer responds to commands. One of the combinations that indicate a breakdown also lights up, but each manufacturer and even each model have them. But there is only one result - during the washing process (no matter what stage) the machine stops and no longer responds to any signals. Sometimes it can be started again. But after turning it on, it stops again.
The fact is that there is a leakage protection sensor in the pan - this is a polystyrene float. When water appears in the pan, it rises, the contact closes, which is perceived as an alarm. Everything is logical - if water appeared in the pan, then something is going wrong. This float prevents flooding of your apartment and neighbors from below.
Here are the possible causes of PMM water leaks:
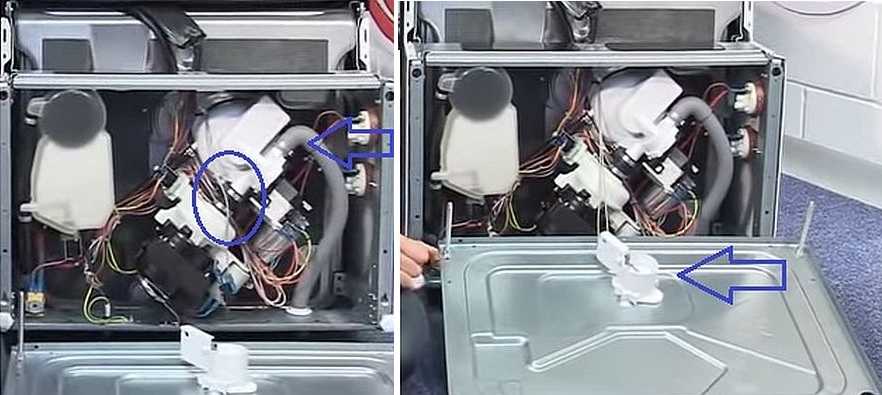
Sometimes a water leak in a dishwasher is a consequence of a leak in one of the parts. Then you need to remove the back wall of the dishwasher, carefully inspect all the details. There may be a leak in the hose, the connection has lost its tightness, etc.
No drain
There are malfunctions of dishwashers of the opposite nature - PM does not drain the water. There are reasons of a different nature. This type of breakage is often associated with a clogged drain hole or hose. Here's what could be:

If the problem is a blockage in the machine, first clean the drain and filter. Next, remove the pump cover. This is a plastic cover secured by bolts (bolt). In some brands, it is fixed with latches. We clean the impeller and impellers (holes for spraying water). In general, we remove all residues and contaminants that catch our eye. The cleaner the car, the less likely it is to stop again.
If you are repairing a dishwasher with your own hands and you have little experience in this matter, photograph the position of all parts and parts before you begin to disassemble the unit. It will be easier to restore everything. Even if it seems that there is nothing to forget.
We set everything in place, turn on the car. Water drainage should be restored. If not, there may be a reason for the pump. It does not pump water and should be replaced.
No water is coming in or little water is being collected.
Dishwasher problems are often water related. And one of them - little water is collected. It may still be - the detergent is not washed off, it does not rinse well. All these malfunctions of the dishwasher can be caused by one reason - insufficient pressure. It is checked first of all. The pressure in the system should be above the minimum threshold at which the PM can be operated (in the passport). If the pressure is normal, there may be the following reasons for this failure:
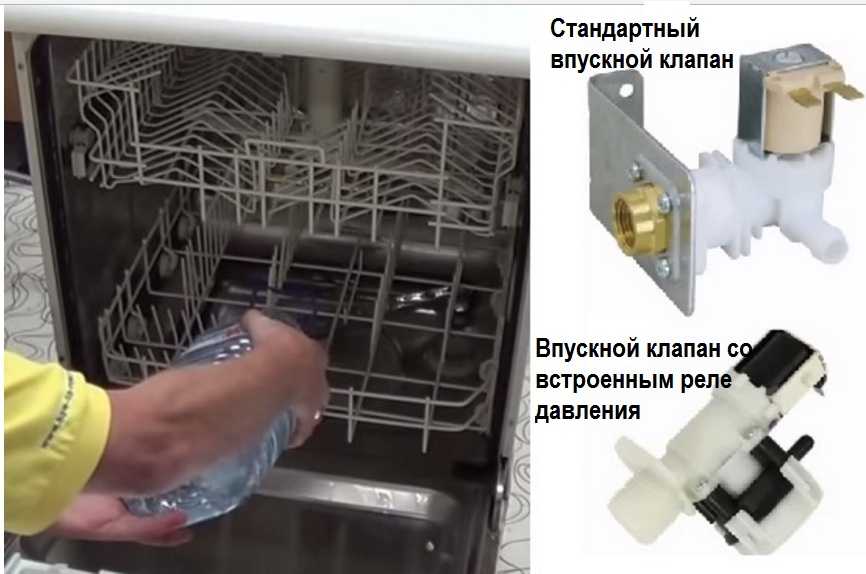
To make sure that the problem is in the water supply system, and not in others, pour 4 liters of water into the machine, load some dishes and start. If the machine is not washing, most likely the malfunction of the dishwasher is related to control.
It washes badly
Sometimes, after some time after the start of operation, you notice that the dishwasher washes dishes worse. Such malfunctions are usually associated with a violation of the operating rules, but there may also be technical problems. So, what could be the reasons that the quality of washing up has deteriorated:
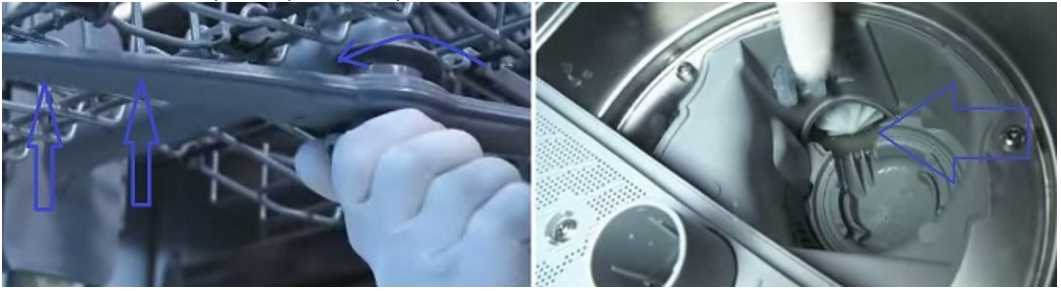
Dishwasher malfunctions related to poor quality can also be caused by malfunctions. If you checked all the possible causes, and the improvements are imperceptible, follow the process. You may be able to understand why the dishwasher has become worse than washing dishes.
Knocks out a circuit breaker
Dishwasher-related electrical problems usually occur after power surges. Then the "crashes" and management. Therefore, during installation, it is advisable to attend to the installation of the stabilizer. If not common - the whole apartment or house, then at least local. It can be a low-power unit for connecting a dishwasher, or it can be a more powerful one, to which several devices with electronic control can be connected.
If you turn on / start the dishwasher and knock out the circuit breaker in the panel, the reasons may be the following:
- Blown heater.
- Closing wiring inside the PM.
- Sealing is broken and water gets on the parts.
- Voltage drops in the network.
Identifying the exact cause of most of these malfunctions (other than a breach of the seal) suggests that you know how. Take the electrical circuit of the dishwasher, first check the condition of the fuses, then move along the circuit.
These are, perhaps, all the main malfunctions of dishwashers, which can be fixed with your own hands. If these measures do not help, you will have to resort to the services of specialists.
Related videos
List of malfunctions of dishwashers. Do-it-yourself repair methods. How to repair a dishwashing machine? We repair an automatic dishwasher. (10+)
Faults and repair of dishwashers
Dishwasher (PM) is a fairly simple unit. Many of its malfunctions can be diagnosed and eliminated independently. Let us dwell on them in more detail.
Water does not heat up
Heating in the PM is carried out by a heating element installed at the bottom of the chamber for dishes. Complex models are equipped with a temperature sensor, which allows the machine to heat water to a certain temperature in accordance with the selected mode. Simple models include this heating element for a certain time without any feedback. During this time, the water heats up as much as it has time.
In machines with a temperature sensor, if the element burns out, operation ceases altogether, since the water cannot heat up to the desired temperature, the temperature sensor does not work, and the washing process cannot be continued. This malfunction can be determined by the behavior of the machine. It is filled with water (a characteristic sound is heard), then it starts to heat the water, and then the car dies, nothing happens. Some machines have a fuser burnout indicator.
In machines without a temperature sensor, burnout of the heating element does not stop the machine. The machine continues to wash the dishes with cold water. The quality of the wash, of course, drops sharply. You can determine the malfunction by opening the machine after a dishwashing cycle. The dishes and the inside of the machine should be quite warm. You can also touch the outlet of the machine during the first discharge of water. It must be warm. If the dishes and the branch pipe are cold, it means that the heating element has failed or the automation that controls it is faulty.
Automation cannot be repaired by ourselves. But the heating element can be replaced. Let's check it out first. Turn the car over. Remove the bottom, if it is. Looking into the chamber for dishes, we find a heating element. He stands at the bottom of the camera (now, in the new position of the machine, he is at the very top), and his contacts and the mounting unit are displayed through the bottom. Contacts are wired. Some elements are connected with a clip; some wires are screwed with nuts. In any case, turn off the wires and measure the resistance of the element with a tester. The tester should show the presence of conductivity.
If there is no conductivity, the heater (thermal element) is clearly defective. It is easy to remove. It is fixed with several bolts or self-tapping screws. We unscrew them from the bottom and take out the heater from the side of the chamber for dishes.
Electric shock
With a probability of 99%, the heater is also to blame. It struck. We remove the thermal element, inspect. Typically, cracks and defects are visible by visual inspection. You can place the element in salt water and measure the resistance between one of its electrodes and a salt solution. The presence of conductivity indicates a breakdown. However, this method of measurement does not always give the correct result. In some rare cases, a punctured heater does not show conductivity.
The cause of burnout or breakdown of the heater is usually too hard water and neglect of the use of salt for regeneration of the softener.
Water overheats
Steam begins to pour out of the machine some time after water has been collected. Washing does not start. The water temperature sensor or the brains that control the heating element are out of order. Such a brain malfunction theoretically occurs, but in practice I have never seen it. The sensor is usually defective.
Water does not pour
There may be several reasons. At firstWater supply valve defective. This valve is installed directly behind the water supply pipe from the water supply. It usually together with this pipe forms a monolithic, non-separable structure. Secondly, the mesh that is installed between the hose from the water supply pipe and the inlet pipe is clogged. ThirdlyThe water level sensor is faulty. All the time, it seems to the car that the water has already poured.
First, check and clean the mesh, as this is easiest. If this does not help, then remove the valve and check it with a tester. Conductivity must be present. If there is conductivity, read what is written on this valve. If it is designed for 220V, then it can be very carefully (so as not to get under voltage itself), plug into the network and make sure that it opens, for example, by blowing into it. If it is designed for a different voltage, then this voltage must be supplied. On some machines, this valve is powered by a 12 volt brain supply voltage. But such valves are a rarity. Usually 220V is supplied. It is clear that if 220 is applied to a 12-volt valve, it will burn immediately.
If the matter is not in the mesh and not in the valve, then the level sensor is faulty. Here I want to upset you, in the event of a level sensor malfunction, the heater usually burns out immediately.
Water does not drain
Defective water draining unit (valve and pump). They should be replaced. Usually this is a single unit.
Water overflows
Some time after turning on, water begins to flow from all the slots from the machine. Defective level sensor. But, unlike the previous version, it now shows a constant lack of water. This malfunction is unpleasant from the point of view of the neighbors' bay from below, but not dangerous for the heater. This sensor is usually installed at the bottom of the machine. Turn the dishwashing machine over, remove the bottom cover and replace the sensor.
The dishwasher does not wash the dishes
The machine turns on, fills with water, heats the water. But then the characteristic sound of washing is not heard. No streams of water. There may be three reasons. At first, the filter is clogged. The filter is located at the very bottom of the cooking chamber. It must be opened and rinsed. Secondly, nozzles in the combs clogged. Nozzles can be cleaned with a toothpick. Thirdly, the circulation pump has broken, which drives water from the bottom of the bowl into the nozzles and ensures washing the dishes. This pump works with a distinctive sound when dishes are washed. If there is no sound, the pump is probably broken. You can replace the pump yourself. It is installed under the bottom of the bowl. Power is supplied to it by a clip; water is supplied and discharged through tubes that are put on the pump inlet and outlet nozzles and secured with clamps. The clamps must be removed, disconnect the tubes. The pump is mounted with one or more self-tapping screws. Unscrew them and remove the pump. Installation is in the reverse order.
Unfortunately, errors are periodically found in articles, they are corrected, articles are supplemented, developed, new ones are prepared. Subscribe to the news to stay informed.
If something is not clear, be sure to ask!
Ask a Question. Discussion article. messages.
The problem with the dishwasher. Stopped working in the middle of the program. The filter removed the water and cleaned the nozzles. I turned it on, I got water, the pump does not work (the machine does not supply water to the blades). Disconnected from the network, drained the water connected - ignores the lack of water, the heating element warms up to dry.
Serving a dishwashing machine ...
Installation, connection and operation of the dishwasher. What are the flaws ...
Knitting. Autumn foliage. Drawings. Pattern schemes ...
How to knit the following patterns: Autumn foliage. Detailed instructions with explanations ...
Knitting. Waffles. Striped shadows. Strings along the back field. Drawings ...
How to knit the following patterns: Waffles. Striped shadows. Wrong sewing strings
Knitting. Zigzag arrows. Bows. Drawings. Pattern schemes ...
How to knit the following patterns: Zigzag arrows. Bows. Detailed tool ...
Knitting. Diagonal Flower fantasy. Tight stripes. Drawings ....
How to knit the following patterns: Diagonal. Flower fantasy. Tight bands ...
Knitting. From one loop, knit three loops. Drawings. Pattern schemes about ...
How to knit three loops from one loop. Examples of patterns with such loops ...